GRP Roofing Products And Contracting Services By Guaranteed GRP
“The Fibreglass Roofing Specialists”
Guaranteed GRP are the fibreglass roofing specialists, offering a premium range of GRP roofing products alongside expert installation services across the UK. Their product line includes high-performance GRP resins, topcoats, trims, and roofing kits, all developed to deliver superior durability and weather protection. These systems are designed for flat roofs, balconies, walkways, and complex detailing, ensuring seamless waterproofing and a clean, professional finish. Every item is manufactured to meet strict quality standards, providing long-term resistance against UV exposure, standing water, and temperature fluctuations common across the UK. Guaranteed GRP’s in-house contracting team applies these products with precision, using proven techniques to maximise product performance. Whether supplying materials for contractors or delivering a complete roofing system, Guaranteed GRP ensure dependable results. Guaranteed.
What Is GRP Roofing?
GRP roofing, short for Glass Reinforced Plastic roofing, is a durable, seamless fibreglass roofing system commonly used on flat and low-pitched roofs. It is made by layering fibreglass matting with a liquid resin, which cures to form a solid, waterproof surface. Originally developed for marine and aerospace use, GRP is now popular in roofing due to its exceptional strength, flexibility, and resistance to weathering. Unlike traditional felt or bitumen systems, GRP contains no joints or seams, reducing the risk of leaks. It offers a sleek, modern finish and can be moulded around complex roof shapes, including upstands and trims. GRP roofs require minimal maintenance and typically last 25–30 years when properly installed. They are ideal for both residential and commercial applications, especially in areas prone to heavy rainfall.
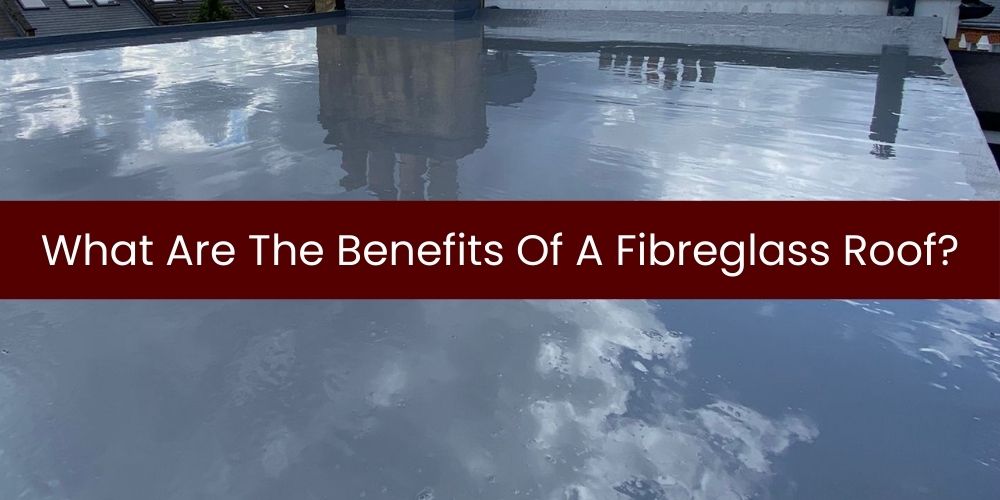
What Are The Benefits Of A Fibreglass Roof?
A fibreglass roof offers a strong, seamless, and long-lasting waterproofing solution ideal for flat and low-pitched roofs. Its resistance to weathering, UV exposure, and foot traffic makes it a practical choice for both domestic and commercial properties. With minimal maintenance and a sleek, modern finish, fibreglass roofing delivers long-term performance and aesthetic appeal.
- Seamless and fully waterproof surface
- Long lifespan (typically 25–30 years)
- Resistant to UV, extreme weather, and fire
- Durable under regular foot traffic
- Low maintenance requirements
- Clean, modern appearance
- Easily moulded to complex roof shapes
- Ideal for extensions, balconies, and walkways
1. Seamless and fully waterproof surface
GRP roofing systems are laid as a single continuous membrane, meaning there are no seams, joints, or weak points where water can penetrate. This seamless construction significantly reduces the risk of leaks, especially compared to felt or bitumen systems that rely on overlapping layers. Once cured, the fibreglass surface forms a complete waterproof barrier, ideal for protecting flat roofs from standing water. This makes it especially suited to the UK climate, where prolonged rainfall can challenge traditional roofing materials.
2. Long lifespan (typically 25–30 years)
One of the most appealing qualities of a fibreglass flat roof is its exceptional longevity. When correctly installed and maintained, a GRP roof can last between 25 and 30 years without significant deterioration. The materials used are highly resistant to weathering, corrosion, and general wear, which extends the roof's service life far beyond that of many traditional systems. This long-term durability offers excellent value for money over time, reducing the need for frequent repairs or early replacement.
3. Resistant to UV, extreme weather, and fire
Fibreglass flat roofs are engineered to resist damage from ultraviolet rays, making them ideal for both sunny and harsh weather conditions. Unlike some roofing systems that crack or degrade under prolonged sun exposure, GRP maintains its structural integrity. It also performs well in freezing temperatures, heavy rainfall, and high winds, making it a reliable solution across seasonal extremes. Additionally, GRP is fire-retardant and complies with UK fire safety standards, offering an extra layer of protection for properties.
4. Durable under regular foot traffic
Unlike other flat roofing materials which may puncture or deteriorate under footfall, GRP is highly resistant to impact and wear. Once cured, it forms a rigid, non-slip surface capable of handling routine access for maintenance, cleaning, or even recreational use on balconies and terraces. This makes it especially beneficial for flat roofs which may need to support tradespeople, plant equipment, or foot access without compromising the integrity of the waterproof layer. Its robustness also reduces the risk of accidental damage.
5. Low maintenance requirements
A GRP roof requires very little maintenance compared to traditional roofing options. The non-porous surface resists moss, algae, and dirt build-up, which means it retains its appearance and performance with minimal cleaning. There’s no need for regular recoating or patching, and periodic visual inspections are usually sufficient. This low maintenance demand makes it a practical and cost-effective choice for both homeowners and commercial property managers.
6. Clean, modern appearance
The finished surface of a GRP roof is smooth and sleek, offering a neat, contemporary look that enhances the appearance of modern builds and refurbishments alike. It can be coloured with pigmented topcoats to match or complement existing architecture. The uniform finish also gives it a high-quality aesthetic compared to systems that use felt or bitumen. This makes GRP popular for visible roof areas, such as extensions, garden rooms, and balconies.
7. Easily moulded to complex roof shapes
GRP is a versatile material which can be applied to roofs with intricate layouts, upstands, parapet walls, and embedded features like skylights and vents. The resin and matting can be shaped and layered to suit almost any form, providing a watertight seal around details that other systems struggle to accommodate. This adaptability makes it ideal for bespoke architectural projects or renovation work where traditional materials might fall short. The result is a consistent, watertight finish, even on complex surfaces.
8. Ideal for extensions, balconies, and walkways
Due to its strength, watertight finish, and aesthetic versatility, GRP is especially well-suited to roof areas with high visibility or practical use. It’s commonly specified for home extensions, flat roof balconies, and rooftop walkways where both performance and appearance are key. Its ability to withstand foot traffic, resist ponding water, and maintain a clean finish over time makes it a standout choice for such applications. This makes fibreglass a favourite among architects, contractors, and property developers alike.
Want a price for a project?
What Are The Best Products For Fibreglass Roofing Kits?
The best products for fibreglass roofing kits are highly elastic hybrid GRP systems such as Fibre Pro. Fibreglass roofing kits are complete systems typically made up of resin, topcoat, fibreglass matting, and detailing trims used to create seamless, waterproof flat roofs.
Fibre Pro stands out because it combines the structural integrity of glass fibre reinforcement with the flexibility of advanced polyurethane technology, overcoming the traditional brittleness often associated with standard GRP systems. Its elasticity allows it to adapt to structural movement and ageing surfaces, while still delivering the watertight performance expected from a professional-grade fibreglass system—making it ideal for commercial, industrial, and residential roofing projects.
The characteristics to look for in GRP roofing products when choosing a fibreglass roofing kit are:
- Elasticity and Flexibility
- High-Quality Glass Fibre Reinforcement
- Crack-Bridging Performance
- UV and Extreme Weather Resistance
- Installer-Friendly Application
- Thixotropic Properties
- Multi-Surface Compatibility
- Low VOC and Environmentally Safer Composition
1. Elasticity and Flexibility
Elasticity is a critical factor in modern GRP roofing kits, especially when applied to structures subject to thermal movement or minor shifting. Unlike traditional systems that can become brittle with age, advanced GRP roofing kits offer enhanced flexibility, allowing the membrane to move with the building without cracking. This is essential for maintaining watertight integrity over time. Flexibility also supports installation on more complex surfaces or roof designs where some movement is inevitable.
2. High-Quality Glass Fibre Reinforcement
The strength and longevity of GRP roofing kits are heavily influenced by the quality of the glass fibre reinforcement included. Kits with high-grade woven or chopped strand matting provide better tensile strength, impact resistance, and dimensional stability. These reinforcements enable the cured system to span wide roof areas without stress fractures or sagging. The correct pairing of matting with compatible resins is vital for the durability of the finished roof.
3. Crack-Bridging Performance
Crack-bridging is an essential feature for GRP roofing kits being used on aged or uneven substrates. This capability allows the system to maintain a waterproof seal even when minor cracks or surface imperfections exist beneath. It adds a level of resilience that’s especially important during refurbishments or overlays. A roofing kit with strong crack-bridging performance reduces the risk of future water ingress due to substrate movement.
4. UV and Extreme Weather Resistance
GRP roofing kits must be engineered to withstand the full range of UK weather conditions, from prolonged UV exposure to driving rain and frost. UV resistance prevents premature degradation, colour fading, and surface chalking, ensuring the system retains its finish and performance. Resistance to freeze-thaw cycles and standing water also ensures long-term protection. Quality kits maintain their structural integrity regardless of seasonal extremes.
5. Installer-Friendly Application
Time-saving features are important when choosing GRP roofing kits, particularly for commercial projects or where weather conditions limit installation windows. Installer-friendly kits often use single-component or moisture-cured formulations that simplify the process and reduce the margin for error. Quicker curing times and consistent application performance help ensure reliability and reduce labour costs. These qualities are especially valuable for contractors managing large-scale installations.
6. Thixotropic Properties
Thixotropic resins, common in premium GRP roofing kits, hold their form once applied and resist sagging, even on vertical or detailed surfaces. This is crucial when applying resin around trims, upstands, outlets, and roof edges. A thixotropic formulation ensures controlled coverage and consistent membrane thickness. It contributes to a cleaner, more professional finish and improves the accuracy of detail work during installation.
7. Multi-Surface Compatibility
High-quality GRP roofing kits are designed to bond securely with a wide range of common substrates including timber, concrete, OSB3 boards, and even insulation. Kits that do not require specialist primers can save time and reduce complexity during installation. This versatility is vital on refurbishment projects where surface materials may vary. Reliable adhesion across all surfaces ensures a uniform, durable finish.
8. Low VOC and Environmentally Safer Composition
Modern GRP roofing kits increasingly feature low-VOC resins to improve on-site safety and reduce environmental impact. These formulations emit fewer harmful fumes, making them safer for installers—especially in confined or poorly ventilated areas. Additionally, they help projects comply with environmental regulations and sustainability standards. Selecting kits with environmentally conscious chemistry is now a best practice in professional roofing specification.
Fibre Pro meets all the above criteria, making it an outstanding choice for GRP roofing kits. Its advanced formulation delivers superior elasticity and flexibility, allowing it to accommodate structural movement without compromising waterproofing. Reinforced with high-grade glass fibres, it offers excellent crack-bridging capability and impact resistance. Fibre Pro is built to withstand UV exposure and harsh weather, while its one-component, thixotropic nature ensures ease of application—even on vertical or detailed surfaces. It adheres to a wide range of substrates without additional primers and is manufactured with a low-VOC, environmentally responsible composition. Whether used for new installations or refurbishment projects, Fibre Pro delivers consistent, professional-grade performance across every aspect of GRP roofing.
What Is The Installation Process Of A Fibreglass Roof?
The installation process of a fibreglass roof involves preparing the roof deck, applying a base coat of resin with glass fibre matting, and finishing with a topcoat for UV protection. First, the deck is cleaned, primed, and fitted with trims. The resin and matting are then laid in layers to form a seamless, reinforced waterproof membrane. Once cured, a coloured topcoat is applied to seal the surface and protect against weathering, completing the GRP roofing system.
The steps for a fibreglass roof installation are:
- Prepare the Roof Deck
- Install Edge Trims and Detail Work
- Prime the Surface (If Required)
- Apply Base Coat of Resin and Reinforcement
- Allow the Base Layer to Cure
- Inspect and Lightly Sand (If Needed)
- Apply Coloured Topcoat
- Allow Final Curing Before Use
1. Prepare the Roof Deck
Begin by ensuring the roof deck is clean, dry, and securely fixed. Any loose boards must be reattached, and the surface should be free from dust, grease, or debris. The deck must be constructed from suitable material, typically OSB3 or plywood, and installed with adequate fall to promote water runoff. A solid, well-prepared base is crucial for the long-term performance of the fibreglass roofing system.
2. Install Edge Trims and Detail Work
GRP-compatible edge trims should be fitted around the perimeter of the roof and any upstands. These trims manage water flow and give a clean, finished edge to the roof. Fixings must be secure, and corners properly mitred or jointed to ensure a professional finish. Proper detailing at this stage prevents future water ingress and ensures a neat result.
3. Prime the Surface (If Required)
Some substrates, particularly those with porous or uneven surfaces, may require a primer to enhance resin adhesion. The primer should be compatible with the resin system being used and must be allowed to dry completely before proceeding. This step improves bonding and helps create a smooth base for the subsequent layers.
4. Apply Base Coat of Resin and Reinforcement
Roll out the glass fibre matting onto the prepared surface and saturate it evenly with resin using a roller. Work in manageable sections, and use a consolidating roller to eliminate air pockets and ensure full impregnation of the mat. This forms the main waterproofing layer and reinforces the structure of the fibreglass roof.
5. Allow the Base Layer to Cure
Once applied, the base layer of resin and matting must be left to cure fully before any further work. Curing times will vary based on product type and weather conditions, but the surface should become firm and tack-free. This stage is critical to ensure the structural integrity of the waterproof membrane.
6. Inspect and Lightly Sand (If Needed)
After the base layer has cured, check the surface for raised fibres, sharp edges, or imperfections. If necessary, lightly sand these areas to ensure a smooth, uniform finish before applying the topcoat. This step helps the topcoat adhere evenly and improves the appearance of the final surface.
7. Apply Coloured Topcoat
Apply the coloured topcoat across the entire roof surface to seal and protect the fibreglass membrane. The topcoat adds UV resistance and weatherproofing while giving the roof a consistent, professional finish. It should be applied in a uniform layer using a roller or brush, following the manufacturer’s guidelines for coverage and curing.
8. Allow Final Curing Before Use
Once the topcoat is applied, allow the roof to cure fully before exposing it to foot traffic or rainfall. Curing time can vary but typically ranges from several hours to a full day depending on ambient temperature and humidity. Full curing ensures the GRP system achieves its intended durability and performance.
Is A Full Fibreglass Flat Roof Installation a DIY Task?
Fibreglass flat roof installation, is generally considered a job best left to professionals. The process requires precise timing, consistent resin application, and knowledge of curing conditions—any errors can lead to poor bonding, leaks, or premature failure. Working with resins and glass fibre also demands protective equipment and good ventilation, as well as an understanding of how temperature and humidity affect curing. For long-term performance and guarantee eligibility, most GRP roofing kits—including Fibre Pro—are recommended for professional installation.
Can DIY Enthusiasts Carry Out Fibreglass Roof Repairs?
Repairs to a fibreglass roof can be successfully carried out by capable DIY enthusiasts, especially when using a product like Fibre Pro. Its thixotropic formulation makes it easy to apply both on flat field areas and upstands without sagging or running, even on vertical surfaces. Fibre Pro also features built-in reinforcement and excellent surface grab, eliminating the need for separate glass fibre matting in many repair scenarios. This simplifies the process and ensures a strong, seamless bond, making it a user-friendly option for straightforward, durable GRP roof repairs.
Want a price for a project?